Choosing the Right Aluminium Powder Coating for Your Industry Needs
The rapid expansion of manufacturing industries in the world has also increased the requirements for more practical, beautiful and cost – efficient coatings. Among various coating solutions, aluminium powder coating is one of the most extensively used because of its durability, environmental benefits, and quality of finish. The aluminium powder coating procedure, if well implemented, would extend the life span and attractiveness of metal products in nearly all sectors. Nevertheless, choosing the appropriate aluminium powder coating for industrial uses must be done with several key factors in mind. This article explains all the primary aspects that should be taken into account when selecting an aluminium powder coating for your national or international industrial applications.
Understanding the aluminium powder coating process

Aluminium powder coating is a process whereby finely ground pigment and resin particles are electrostatically applied to a metal sprayed surface. The powder is charged positively using an electrostatic spray gun and adheres to the metal. Once applied to the metal, the powder is heated in a curing oven, which melts the powder as heat, creating a durable, smooth finish that adheres to the surface.
Several advantages also come from using this method over typical liquid coatings. There is no requirement for the solvents, and this makes the approach environmentally safe. This produces a thicker, more uniform coating that improves product life span, durability, and corrosion resistance. Aluminium powder coating process is particularly useful in construction, automotive and architecture, where both functional durability and aesthetic quality are paramount. This technique produces long-lasting, high-performance finishes that meet demanding industry standards.
Key factors to consider when selecting a coating
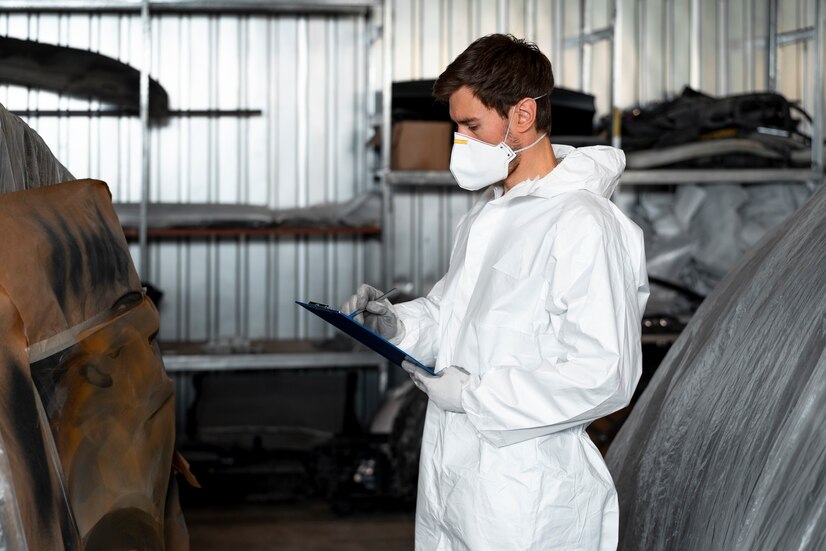
Choosing the right aluminium powder coating for a particular industry is based on countless factors, including environmental exposure, desired durability, and final finish characteristics. Based on these factors, industries, including automotive, electronics and building materials, will have different requirements. As it does, you might have found that an automotive part needs a coating to survive high temperature, chemical exposure, and mechanical stress, while a product for the exterior of a building must resist UV degradation and weathering.
The choice of coating involves environmental conditions. Aluminium powder coatings used outdoors must resist fading, corrosion and damage from the effects of environmental factors such as UV rays, salt or pollutants. On the other hand, indoor applications might tend to emphasize aesthetic properties like smoothness, gloss level, and colour consistency. For this reason, it is important to know the exigencies of handling the finished product, its usage and possible exposure to the environment in one’s industry.
Types of aluminium powder coatings available
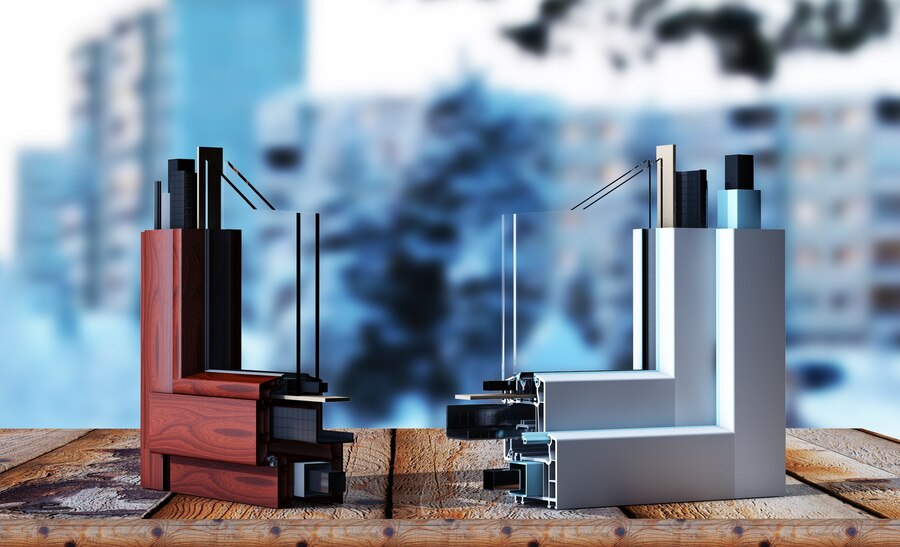
There are several types of aluminium powder coatings, depending on their application requirements. There are two main categories, namely polyester, epoxy and hybrid coatings. UV and weather resistance are key traits of polyester coatings, and they work very well for outdoor applications such as construction and signage. While epoxy coatings are known for their superior corrosion resistance, they are ideal for indoor use, such as automotive and electronics, where chemical durability is critical. These hybrid coatings combine the best of both polyester and epoxy at a reasonable cost, providing a solution for outdoor weathering and indoor corrosion protection. As protection conditions and performance needs vary, the coating that is chosen depends on the product exposure conditions.
Importance of surface preparation in coating success
The aluminium powder coating process requires surface preparation. Even the highest quality coatings can fail to adhere properly without proper preparation, and this can result in poor finish, peeling, early wear, etc. It is important to perform this step because it inv olves cleaning the metallic surface of the work piece with the aim of getting rid of contaminants such as dirt, oils, rust, and particles of solid debris. To produce a clean surface for optimal bonding, methods such as abrasive blasting, sandblasting or chemical cleaning are used. An additional primer or pre-coatings may be applied in some cases to improve adhesion. This also helps ensure a smooth, uniform finish and improves the durability and longevity of the coating. It is, therefore, very important to properly prepare to get the best results and optimize the aluminium powder coating performance.
Environmental considerations in coating selection
With the increase in environmental concerns, the aluminium powder coating industry finds itself shifting towards the production of more eco-friendly solutions. Whereas liquid coatings release harmful volatile organic compounds (VOCs), aluminium powder coatings are almost entirely solvent-free. They are a more environmentally sustainable option. Even more so, many of the powder coatings are now created to be low VOCs. This eco-friendly attribute of powder coating makes it a popular choice for industries where compliance with environmental regulations is important, such as construction and automotive. Low VOC, green coatings are not only a requirement for compliance with regulatory standards but also help companies build a reputation as responsible, forward-thinking brands in today’s eco conscious marketplace.
Cost-effectiveness and long-term value
Even though the application of aluminium powder coatings may cost more initially than other finishes, they provide extraordinary long-term value. The increased wear and impact fading, scratching, corrosion, and UV degradation-resistance confirmed by powder coatings makes their lifetime longer, thus requiring maintenance to a lesser extent. This is especially critical in industries such as automotive, aerospace, and construction, where lifetime is all the more crucial.
Additionally, the powder coating process is more efficient and economical than painting. The coating is applied in one step and produces minimal waste, as well as very few touch-ups or rework. It also needs less time and energy for curing, which helps bring down production costs. Over time, reducing production expenses and maintenance costs makes aluminium powder coating financially viable for many industries.
Conclusion
When determining the best aluminium powder coating for industrial uses, the user must ensure both the durability of the metal product and its visual appearance. To enable businesses to make informed decisions on coatings to meet their specific needs, it is important to understand the aluminium powder coating process, and all that is made available in terms of coatings. Manufacturers can select the best coating by taking into consideration factors like surface preparation, environment of use, and cost of long-term effectiveness. The aluminium powder coating industry has seen a marked advancement as options become more diverse and eco-friendly than ever, and businesses can achieve performance coatings with lower environmental footprints.